All About Spiral Wounds
What is a Spiral Wound Gasket?
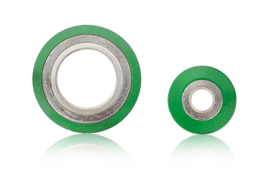
Spiral wound gaskets are designed to provide reliable sealing in industries that require high performance and durability, such as the oil and gas, petrochemical, and refinery sectors. These gaskets are made of metal and are capable of withstanding extreme temperatures, high pressures, and chemical exposure. They are commonly used in industrial plants to prevent leaks and ensure a long lifespan.
How are Spiral Wound Gaskets Made?
Spiral wound gaskets are designed to provide a reliable seal for industrial applications. They are made up of three main components: an outer ring, a spiral ring, and an inner ring.
Spiral wound gaskets are made by winding a strip of metal and a strip of filler material around a mandrel to create a spiral-shaped ring. The metal strip acts as a reinforcement to provide structural support and prevent the gasket from losing its shape, while the filler material helps to seal the joint and prevent leaks. Once the winding process is complete, the gasket is cut to size and then coated with a layer of sealant to enhance its sealing performance. The specific materials used for the metal strip and filler, as well as the type of sealant applied, can be customized to meet the specific requirements of the application.
Meaning of the Rings
The Outer Ring
The outer ring, also known as the centering or guide ring, is used to properly position the spiral wound gasket within a bolted flange joint. It helps to center the gasket and ensure that it is correctly aligned when being installed. The outer ring is typically made of carbon steel, which is a strong and durable material that can withstand high pressure and temperature. The bolts on the joint help to hold the gasket in place and ensure that it stays properly positioned during use.
The Sealing Element
The sealing element, also known as the spiral winding, is the part of the spiral wound gasket that provides the actual sealing function. It is made up of a combination of filler material and spiral winding layers, which work together to prevent leaks. The filler material is usually made from a high-temperature resistant material such as PTFE or flexible graphite, and is specifically chosen to meet the demands of the oil and gas industry. The spiral winding layers provide additional structural support and help to maintain the shape of the gasket. Together, these elements create a reliable seal that can withstand high temperatures, pressures, and chemical exposure.
The Inner Ring
The inner ring is a crucial component of a spiral wound gasket, as it helps to protect the gasket from damage and ensure its longevity. This ring helps to prevent buckling or other types of damage to the gasket, which could potentially lead to issues in the pipeline or pump. While the inner ring is not always required, it can be especially useful in high-pressure sealing situations or environments where the gasket may be subjected to movement or impact. By protecting the filler material and other parts of the gasket, the inner ring helps to ensure that the gasket remains effective and can maintain a reliable seal over time.
Spiral Wound Colors
The color of a spiral wound gasket can provide important information about its composition and properties. In the industry, gaskets are often color-coded to make it easier to identify their materials and characteristics. With spiral wound gaskets, there are typically two different colors: one for the outer rim and another for a stripe along the rim. By using a color guide, it is possible to quickly and easily determine what materials the gasket is made of. This can be useful for selecting the appropriate gasket for a given application and ensuring that it meets the necessary performance requirements.
In the oil and gas industry, you’ve seen these gaskets before. The outside rim is usually yellow (304 SS), green (316 SS), or orange (Monel). All these materials are great for this type of industry as they seal at high temperatures and pressures. The rim stripe is usually gray (Graphite) in the oil and gas industry.
Each material has its own set of advantages that help the gasket seal better in a wide range of environments.
What To Know When Installing Spiral Wound Gaskets
Installing spiral wound gaskets can be a challenging task, but there are steps you can follow to ensure a proper installation. Before you begin, it is important to consult with the manufacturer of the gasket to make sure you are following the correct procedure.
To start, clean and examine the flange, removing any debris or material that may interfere with the fitting of the gasket. Align the flanges so that they are parallel to each other, taking care to avoid excess spacing between the two flanges. If the spacing is more than twice the thickness of the gasket, you should seek the advice of an engineer. Do not over-tighten the flanges, as this can cause damage to the gasket.
Next, inspect the spiral wound gasket for any defects, debris, or damage. Insert a few bolts through the flanges to help align and center the gasket, then guide the gasket onto the flange. Make sure to lubricate the load-bearing surfaces, but avoid applying lubricant to the gasket or sealing surface.
Once the gasket is properly placed, it is time to finish the installation by tightening the bolts. Check to make sure that the bolts are capable of handling the required level of stress and torque, and use a crisscross pattern to tighten them in stages: first hand-tighten them by 20%, then use a torque driver to tighten them to 30%, 60%, and 100%. Finally, make a final round to ensure that all the nuts are uniformly tight. This process should take about five rounds to complete.