About APG
APG was founded in 1943 and remains a leading manufacturer and master distributor in the fluid sealing industry. APG is globally recognized as an ISO9001:2015 registered company specializing in the manufacture and supply of quality sealing, coupling and other industrial solutions.
APG’s ability to adopt new technologies, striving for continuous improvement of their processes, and the forming of long-lasting, strategic partnerships have given their distributors a competitive advantage and the capacity to remain relevant in today’s everchanging marketplace.
This, among many other reasons, is why APG has been Trusted since 1943™.
The Challenge
As a company who primarily functions in the fluid sealing industry, APG began meeting with leading medical facility and hospital directors to further understand the shortage of PPE supplies and review processes needed to gain approval for a new product for these locations. Based on these conversations, APG assembled an internal engineering team to create Face Shield prototypes that could meet medical facility needs. This committee evaluated their standard product range and determined the best course of action was converting the already-existing industrial-rated Face Shields to facilitate the needs of the health care community.
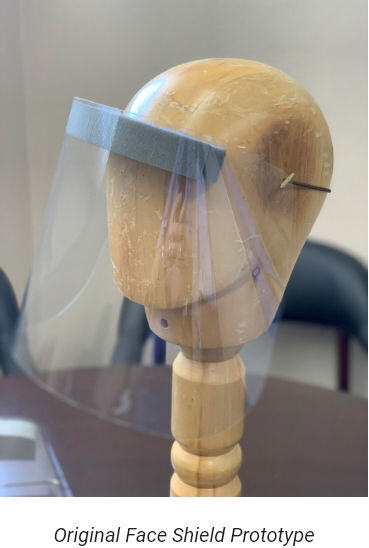
As the engineering team began narrowing down on a proposed design, a sourcing issue became apparent around the growing lack of PETG plastic and available elastic straps needed for the Face Shield’s headband. Matthew Dunn, CEO – APG, began conducting sourcing exercises to acquire these materials and to open new avenues for future material acquisition for the Face Shield manufacturing process. It was also during these exercises APG was able to repurpose existing raw materials from other applications to be used as the forehead cushion which would be comfortable for all day use.
After APG designed and constructed a working prototype, it was submitted to the medical facilities’ task force for approval. The task force evaluated the design on overall protection, functionality, and comfort. With the approval from the task force in hand, APG’s engineering team began designing and constructing various jigs to ensure the upcoming manufacturing process could be done efficiently and expediently. APG began manufacture on the Face Shields by taking its conference room and converting it to a full-fledged production facility seemingly overnight.

The Solution
With production in full swing, over the next several months APG realized there was an issue with the adhesive not creating a permanent bond with the plastic Face Shield. After an evaluation period and feedback from front-line medical workers using the Face Shield daily, APG opted to reengineer all the Face Shields manufactured thus far and have them redeployed.
With a second approval from the medical task force, APG began improving the Face Shield by including a new rivet during production ensuring its reliability and satisfaction for medical workers. When asked if he was satisfied with the outcome of APG’s Face Shield solution, Matthew Dunn stated “The outcome, after testing several components, produced a robust and durable mechanical bond without adding significant alteration to our standard manufacturing process. We were able to satisfy our client and protect from line workers fighting COVID-19.”
One of APG’s Core Values as a business is “Service: Our heart is in servicing our customers and communities.” Lonnie McQurter, Commercial Vice President – APG, was responsible for the framework and coordination of the Face Shield initiative with our customers. Lonnie handled the commercial aspects of the projection such as the initial introductions, proposal submittals, and feedback interactions with the local COVID task force. When asked for his opinion, Lonnie stated “In my view, this is a great example of how APG lives up to our core values. Our ability to assist in solving problems and creating solutions for our customers and communities is what sets us apart from others. It is certainly a pleasure to be a part of a business that is committed to helping our local heroes fight COVID-19.”