
What Is A Spiral Wound Gasket
Spiral wound gaskets were developed to meet the high demands of the oil refinery industry. This gasket is widely used in many industries such as oil, gas, and petrochemical industries. This metallic gasket today is used in industrial plants as it can withstand high temperatures, pressures, and chemical attacks while preventing any leaks that could happen during their intended lifespan.
How Are They Made?
Spiral wound gaskets are constructed out of different parts and materials depending on the circumstances the gasket will be in. These gaskets are constructed of three different sections comprising an outer ring, a spiral ring, and an inner ring. Each section can be made of different materials to ensure the best seal for industrial use.
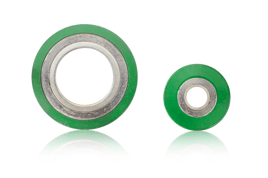

The Outer Ring
The outer ring, sometimes called the centering or guide ring, is used to center the gasket when you insert it into a bolted flange joint. Typically, bolts are on the joint to ensure positioning when placing the gasket on. This outer ring is usually constructed out of carbon steel.
Sealing Element
The sealing element also referred to as the spiral winding, is the area that creates the seal and prevents any leaks. This area also has the filler material and the spiral wounds that create the proper seal. The filler material for the oil and gas industry is usually made from PTFE or a flexible graphite material that is rated for high temperatures.
Inner Ring
The inner ring is an important part of the spiral wound gasket. This section of the gasket prevents and buckling or any sort of damage to the gasket itself. This is important as damage caused to the gasket could go through the pipeline and cause damage internally to the pipe or the pump. This part of the ring is not necessary but will prevent damage to the filler material if thrown around or in high-pressure sealing situations.
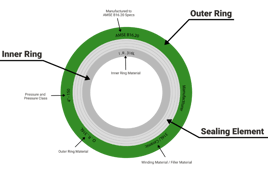

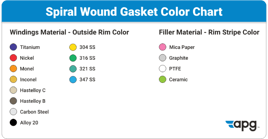
The colors of the gasket do matter! The industry standards require the gaskets are to be color-coded. This helps identify what the gasket is made of quickly and easily. With spiral wound gaskets, there are two distinct colors, the color of the outside rim and the color stripe along the rim. Using our color guide below, you can see the different materials available.
In the oil and gas industry, you’ve likely seen these gaskets before. The outside rim is usually yellow (304 SS), green (316 SS), or orange (monel). All these materials are great for this type of industry as it seals at high temperatures and pressures. The rim stripe is usually gray (Graphite) in the oil and gas industry.
Each material has its own set of advantages that helps the gasket seal better in a wide range of environments.

Installing spiral wound gaskets can be a difficult task. To ensure you install these gaskets properly, here are some tips that will make it easy to get the job done! Before you continue to read these tips, contact the manufacturer of your gasket to ensure the proper steps are taken so you can install spiral wound gaskets!
The first thing you want to do is clean and examine the flange. Dust off any material or debris left on the sealing surface to ensure a proper fitting. Next, you want to align the flanges parallel to each other. Excessing spacing, the space between the 2 flanges is more than twice the gasket thickness, you should stop and consult an engineer. Do not over-tighten think the flanges will come together.
After aligning the flanges, inspect the spiral wound gasket for any defects, debris, or damages. Insert 2-3 bolts through the flanges first, then guide the gasket on the flange. The bolts are there to help align and center the flange perfectly. After loading the gasket on the flange, ensure proper lubrication is applied to the load-bearing surfaces. Do not apply the lubricant to either the gasket or the sealing surface.
Once the gasket is properly placed, it is time to finish the installation and tighten the bolts. Before tightening the bolts, it is important to check if the bolt can handle the level of stress and torque needed for the bolting material. While tightening the nut, ensure the flanges are as parallel as possible to avoid under or over-tightening the bolt. The absolute best way to easily tighten all the bolts is to do a crisscross pattern much like you are with a wheel of a car. This should take about 5 different rounds. 1 round by hand tightens by 20%. For rounds 2-4, tighten with a torque driver of 30%,60%, and 100%. Finally, at the 5th and final round, ensure all nuts are uniform and tight.
APG Wants To Be Your Gasket Supplier
Gaskets come in many shapes, sizes, and materials and you may not be sure where to start when shopping for the products you need! APG can help! Since 1943 we have been providing our clients with the high-quality products they need, as well as assistance in choosing the specific product and material that will work best for their application. Shop our gasket selection now, and if you have questions please don’t hesitate to contact us or look into our knowledge base to help find the right answer. We look forward to exceeding your expectations in both quality and service.

Written By:

Please Fill Out This Form To Be Contacted By An Expert